機能
3次元空間における製品比較検査の位置合わせの重要性
『spGauge』は、製品比較検査ソフトウェアです。検査対象となるのは、製品の現物をスキャンして得た3次元データ(点群)です。その検査で比較対象となるのは、3次元CADデータや他の点群データとなります。
比較検査を行う前に、必ず必要となる作業が「位置合わせ」です。モノとモノを比較するので、重ね合わせる=位置を合わせる、という工程は当たり前に必須となるわけですが、その「位置合わせ」という作業がその後の検査にどのように影響していくか、その重要性について本記事で解説いたします。
3次元空間における製品比較検査の位置合わせとは
spGaugeで行っているような製品比較検査における『位置合わせ』とは、対象となるそれぞれのデータを、それぞれのデータに含まれる物体同士の位置が合うようにデータを動かすことです。
この時、「AをBに合わせにいくために動かす」というように、必ずAとBという対の関係が発生します。これはAが点群データ、Bが3DCADデータの場合もあれば、ABどちらも点群データという場合もあります。
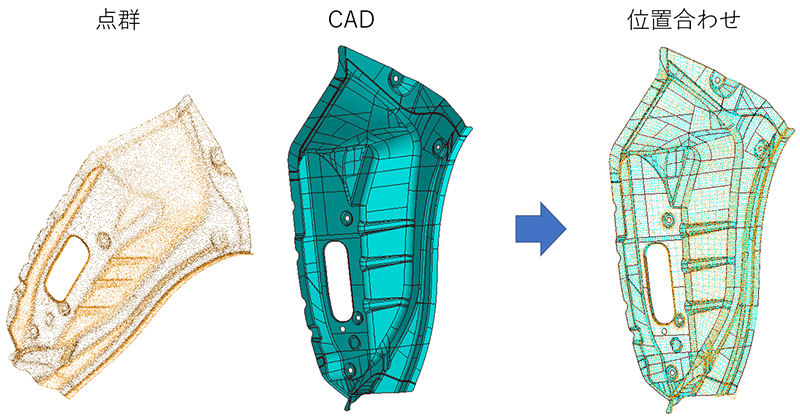
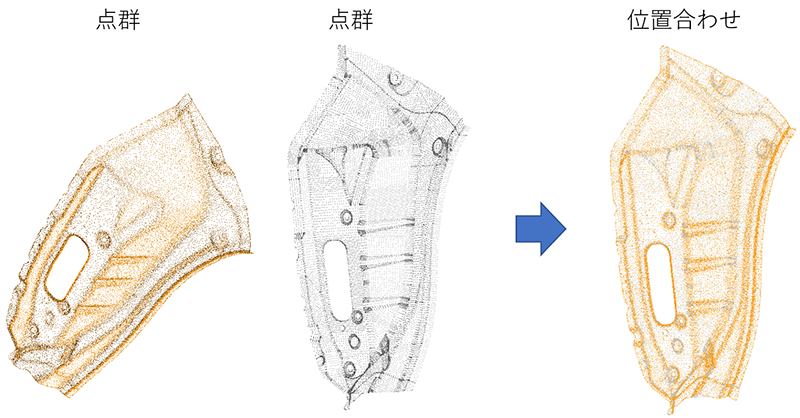
位置合わせの方法は、3次元回転と平行移動によるものになります。
ここで、位置合わせを実現させる方法として、ICP (Iterative closest point) という手法をご紹介します。
Iterative=反復的に
Closest=最も接近した
Point=点
ICPとは、2つのデータ間で以下の2つの処理を交互に繰り返し、移動とペアの探索を同時に行う手法です。
1.片方の点群 (青) から3点以上の点を選び、それぞれの点に対してもう一方の点群 (オレンジ) 内の一番近い点とペアを作る。
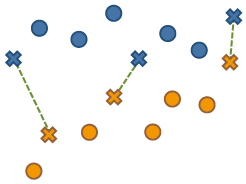
2.最小二乗法を用いて、上記で作ったペアの点同士の距離の2乗の和が最小となるように移動させる。
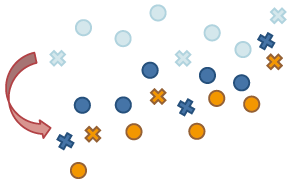
点が移動したことによりペアが変わり、ペアが変わったことにより移動が行われ、2つの点群がさらに近づいていきます。このように、2つの点が重なるまで処理を繰り返していきます。
ICPは一見シンプルですが、とても奥が深い手法です。
対象とする点群の点数や形状などに傾向がある場合は、ペアの作り方や移動の方法を変更することで、その傾向に適した方法に改良することができます。
位置合わせが検査に与える影響
製品比較検査では、上述のように位置合わせを行い対象同士を重ね合わせた後、検査(誤差部を検出)していきます。そのため、“正しく”位置合わせを行うことが、正確な検査では重要になるとわかります。
では、位置合わせにおける“正しく”とは、どのようなことなのでしょうか?正しい位置合わせが出来ているかどうかをどのように判断するのでしょうか。
前章で説明したICPで位置合わせした結果は、対象の形状を全体的に合わせた、概略的なものになります。ラフな言葉で表現するならば、「いい感じに」合わせた結果です。
全体的な傾向を確認するには、この概略的な位置合わせが適していますが、実際の製造現場ではさらに詳細な検査が求められます。その場合には、例えば、他の部品と接する平面や穴を基準として位置を合わせたり、検査治具に取り付けた状態を再現した位置合わせをしたり、検査意図を盛り込んだ様々な位置合わせ方法が必要になります。意図を意識せずに、ただなんとなく位置合わせしただけでは、必要な検査結果が得られません。そのため、位置合わせの段階から、どのような検査を行いたいのか意識することが重要です。
<ベストフィットと基準部位位置合わせの結果比較画像>
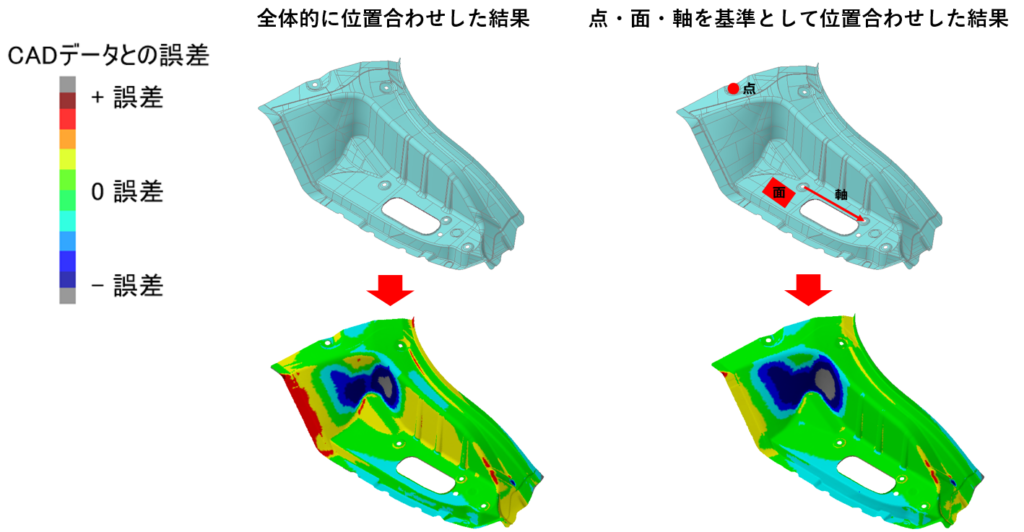
図のように、全体的に位置合わせを行った場合(左)と、ある点・面・軸を基準として位置合わせを行った場合(右)では、検出される誤差の結果(画像では色の出方)に違いが出ます。左は、前述のように全体的な傾向を確認することができます。右のようにある基準で合わせた場合には、その基準位置を正とした場合、どの部位に誤差が出るかを確認することができます。例えば、製品の穴位置をボルトで固定すると、どこがずれるのかという検査ができるということです。
spGaugeの位置合わせ機能(一覧)
検査意図に沿った、“正しい”位置合わせを行うためにspGaugeには多種多様な位置合わせ機能が搭載されています。一般的な機能から、spGaugeにしかないマニアックな機能までありますので、理想の検査が実現できます。
意図した検査を正確に行うためにどのような位置合わせをするべきなのか、spGaugeで最適解が見つかるはずです。サポートチームがご相談も受け付けておりますので、自社の検査方法に課題を感じている方は是非お問い合わせください。