自動化による生産性向上
金型3D形状と加工情報を自動作成
設計から加工まで一気通貫で3Dデータを活用するプレス金型の自動設計システムです。
3Dデータを利用して製造情報を自動出力することで設計工数を従来の1/10に削減しました。
背景と課題

本システムを構築したお客様のビジネスは以下のような特徴がありました。
- 取り扱う製品群は小物プレス部品が中心
- 取り扱う品番が非常に多く、プレス加工を行う製品形状のバリエーションが非常に多い
- 多品種、変種変量の生産に対応する必要がある
この様な状況の中で、他社との競争に勝ち抜くために短納期、低コスト体制を実現する必要に迫られていましたが、当時は設計者が金型図面、各種資料、NCデータ等の全ての成果物を手作業で作成していたため、そのままでは目指す体制の実現が非常に困難でした。
このままではお客様の要求に満足に応えられない、という問題意識が経営層にあり、当時の取締役の方から、デジタルツールを活用して設計プロセスを革新し、金型の設計工数を大幅に削減したい、とアルモニコスにご相談を頂きました。
システム開発のアプローチ方法
最初に、システム化の方針を3次元設計をベースにしたシステム化に決定しました。
これは、3Dデータに必要な情報を集約し、設計から加工まで一気通貫のプロセスを実現することで、後工程で作成する成果物の自動作成が可能になり、大幅に工数削減を削減することができるためです。
その後、以下の3つの方向性を意識して仕様検討を行い、大幅に工数を削減することができるシステムを開発することができました。
- 3Dデータはモデリング機能を使用して作成をせず、標準化したルールを適用して自動作成し、3Dデータの作成工数を削減する
- 形状作成時にチェックを行い、生産要件を満たす形状を作成することで手戻りを防止する
- 3Dデータに必要な情報を付加することで図面やNCデータ等を自動作成し、後工程の成果物作成工数を大幅に削減する
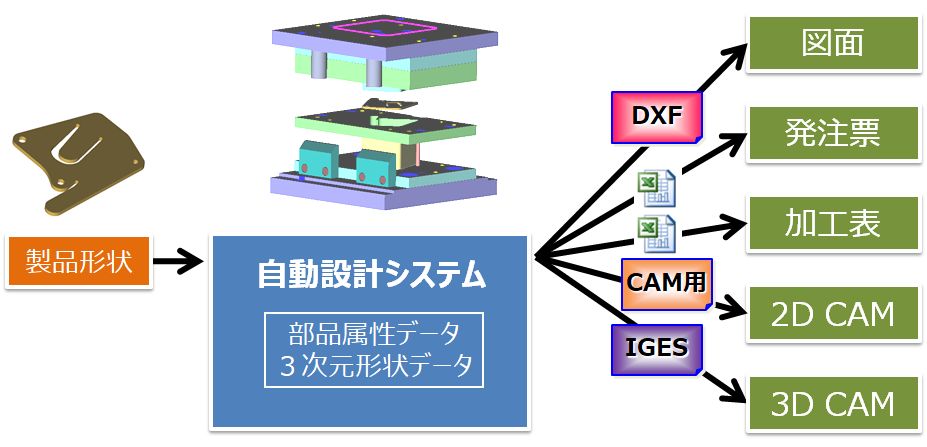
導入効果
3Dデータを活用して設計から加工までをデジタルデータでシームレスにつなぐプロセスに変更したことで、金型の設計プロセスが革新され、大幅な工数削減を実現することができました。
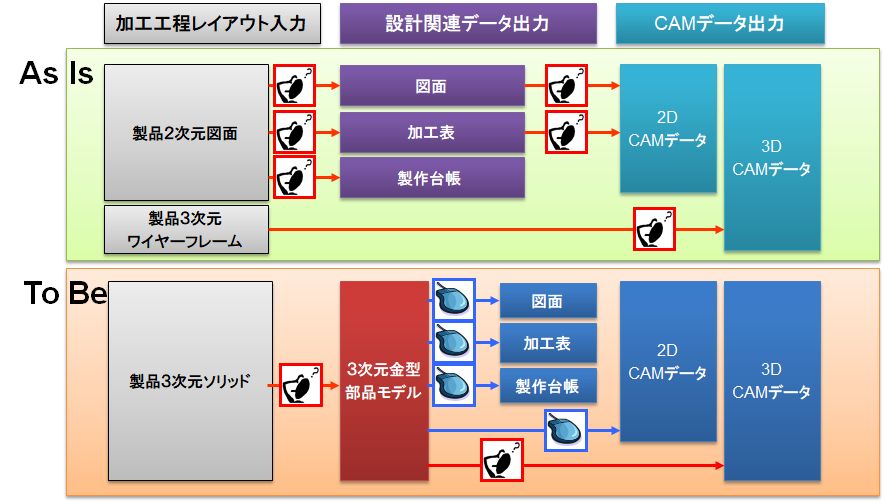
このプロセスの変化により、金型の設計工数が従来の約1/10になりました。また、人為的なミスが0になり、手戻りがなくなりました。
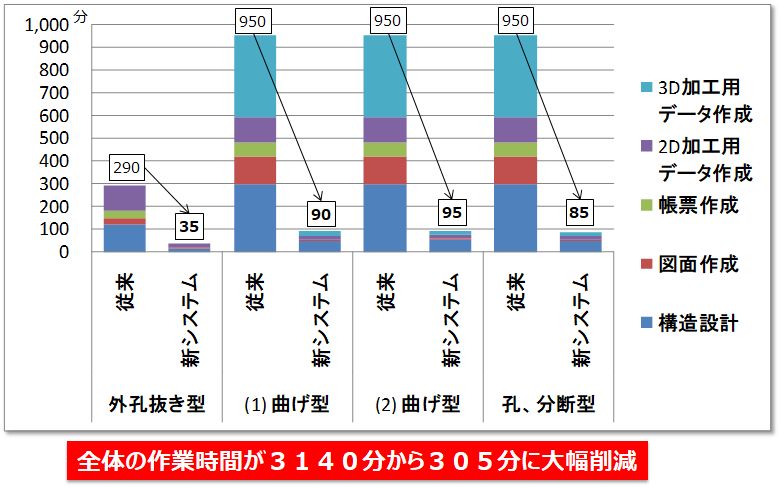
また、以下のような付随的な効果もありました。
- システムを使用することで、経験が浅い設計者でも金型設計が可能になった
- ベテランが難しい技術に取り組む余裕ができ、社内の技術力を引き上げることができた
- 取引先にシステムをアピールすることで取引先からの評価が上がり、受注増、売上増に繋がった