Features
Reducing the volume of CAD data (production line simulation).
Production line simulations use many 3D CAD models. When the original CAD model has complex shapes or numerous surfaces, many meshes must be generated to import them into the simulation system. The large number of meshes significantly deteriorates the simulation system’s overall response.
Therefore, to simulate a large-scale production line system, it is essential to reduce the volume of the CAD data to be used.
Example of unnecessary shapes (1)
Invisible internal shapes
In production line simulations, external shapes are critical, such as whether or not they interfere with each other. Therefore, internal (invisible) shapes are generally unnecessary. Removing unnecessary internal shapes does not change the appearance.
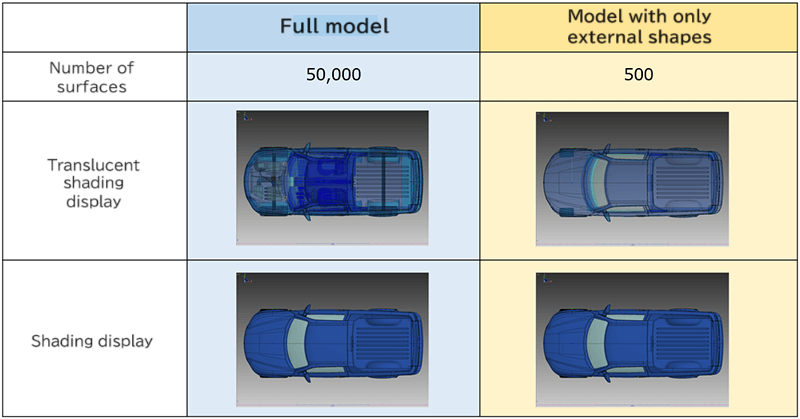
Example of unnecessary shapes (2)
Shapes of small parts (bolts, screws, etc.)
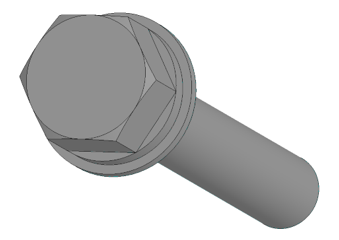
In simulations, the shapes of a large number of smaller, less important parts will significantly increase the overall data volume. In particular, small diameter cylinders or fillets will significantly increase the number of meshes to be created, resulting in poor response.
For example, a set of “one bolt and one washer” requires 648 to 1740 meshes, depending on the conditions. If a model uses a total of 500 bolts, the number of required meshes is 32,000 to 870,000.
A bolt with a washer (M6-L40) | ||
---|---|---|
Number of parts | 3 | |
Number of surfaces | 28 | |
Number of meshes (polygons)* | Maximum edge length: 3 mm | 1,740 |
Maximum edge length: 6 mm | 1,066 | |
Maximum edge length: 10 mm | 972 | |
Maximum edge length: Not specified. | 648 |
Example of unnecessary shapes (3)
Plate with holes
Plates have many hole shapes to allow screws or bolts to pass through. When meshes are generated from the shapes of the plate with holes, there will be many meshes in both the cylinder and the plate.
Depending on the conditions, a plate with holes will generate five times as many meshes as a plate without holes.
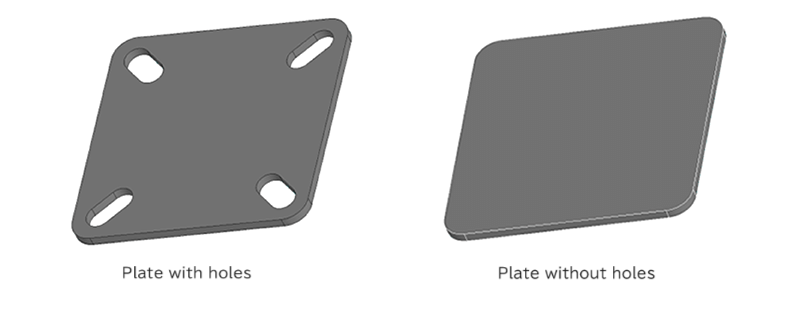
Plate with holes | Plate without holes | ||
---|---|---|---|
Number of parts | 1 | 1 | |
Number of surfaces | 26 | 10 | |
Number of meshes (polygons)* | Maximum edge length: 3 mm | 16,640 | 16,816 |
Maximum edge length: 6 mm | 4,448 | 4,224 | |
Maximum edge length: 10 mm | 1,776 | 1,280 | |
Maximum edge length: Not specified | 700 | 140 |
Example of data reduction effort (1)
Hidden surface removal feature
Automatically removes internal shapes that cannot be seen from the outside.
The removal can be selected either on a “Surface” basis or on a “Part” basis.
It is recommended that “Surface” be selected if you want to reduce as much data as possible.
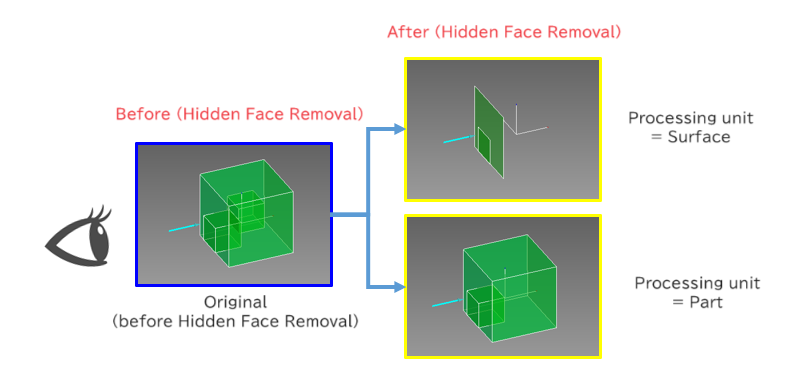
Although the eyeshot axis can be freely set, a number of different eyeshot axes at an equally divided angle are available.
For details, please read the separate article (Lighten the CAD Model with 50,000 Faces to 1/100 of It.).
Example of data reduction effort (2)
Auto Feature Recognition
The system can detect part shapes with the same topological structure (topology), such as screws or bolts, in batches by registering their features with the system in advance. Human error, such as oversight, occurs when unnecessary shapes are manually removed one at a time using a model tree (assembly tree). The Auto Feature Recognition function automatically processes shapes. You can avoid making an oversight by registering all of the unnecessary shapes.
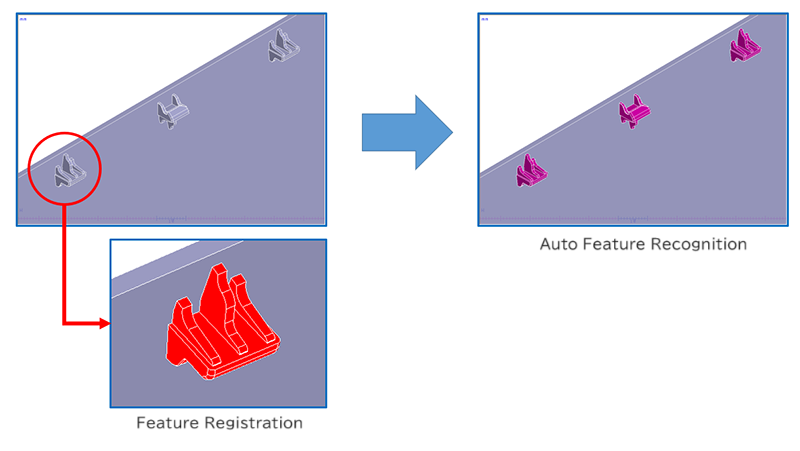
This function changes the colors of the registered faces at once. You can use this function to hide or remove the shapes in batches after verifying them. In “Example of unnecessary shapes (2): Shapes of small parts” above, you can register the features as a STEP file in advance and have the system automatically detect shapes in all CAD models in batches.
tag : data reduction