Use cases
With the Realized Smooth 3D Modeling for Repairs and Remodeling of Existing Ships, Boost Your Competitiveness by Halving Your Construction Period!
Sanwa Dock Co., Ltd., located in Innoshima, Onomichi, Hiroshima, is one of the best proven docks specialized in ship repairs in Japan. It carries out a wide range of repair and remodeling on over 400 ships of all types each year, from coastal vessels to large oceangoing vessels. In recent years, it has been heavily involved in the installation of large equipment, such as ballast water processing systems and SOx scrubbers, that are needed to comply with international environmental regulations, using 3D design methods with 3D laser scanners. A large-scaled new dock that can handle vessels up to 60,000 tons in weight was established in 2016, working on a daily basis to contribute to environmental conservation and safe operation of Japanese or foreign vessels.
On this occasion, Takuya Matsuzaki, general manager of the engineering department, presented the details regarding his adoption of ClassNK-PEERLESS as well as the results it produced.
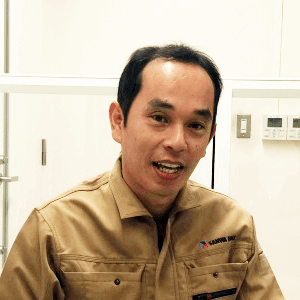
General Manager of the Engineering Dept.
Getting away from reliance on on-site workers to improve quality and reduce construction period
The services offered by Sanwa Dock can be roughly classified into the following three categories.
- General repair work (restoring the ship to its previous state)
- Remodeling work (installing new equipment)
- Engineering work (performing design tasks)
In remodeling and engineering work, accurate understanding of the current state of the already-finished ship is the most important task to do, but back in those days when 3D design technology wasn’t available, this wasn’t possible and a large amount of on-site adjustment was required, which caused such problems as longer construction period and failure to ensure the desired level of quality.
We learned the existence of 3D laser scanners in around 2005, and we sought to somehow use this measurement technology to look for a solution to the aforementioned problems, but with the technology and commercially available software we could obtain at that time, we couldn’t see how to process the measured point cloud data and apply it to on-site work. In particular, due to cost-effectiveness, time constraints, and our enormous work volume, the hurdle to overcome was too high to achieve 3D modeling based on the point cloud data.
We aim for impressive modeling speed, intuitive operation, and tools that can be used even by non-designer operators
In order to solve these issues, we participated from the software design stage and cooperated with the development of a system that would achieve impressive modeling speed and could be operated intuitively by non-specialists including designers. In the end, we decided to adopt the final product, put in practical use as ClassNK-PEERLESS.
At the same time, we introduced the 3D laser scanners and 3D CAD systems required in the upsteream/downstream work of ClassNK-PEERLESS, as well as the equipment and devices for production. Furthermore, we developed a workflow of the following 5 steps: (1) Take 3D measurements of the ship a few months prior to the start of remodeling construction, (2) 3D modeling of the current status using ClassNK-PEERLESS, (3) detailed 3D design, (4) advance production of the necessary parts, and (5) Start actual production with everything prepared.
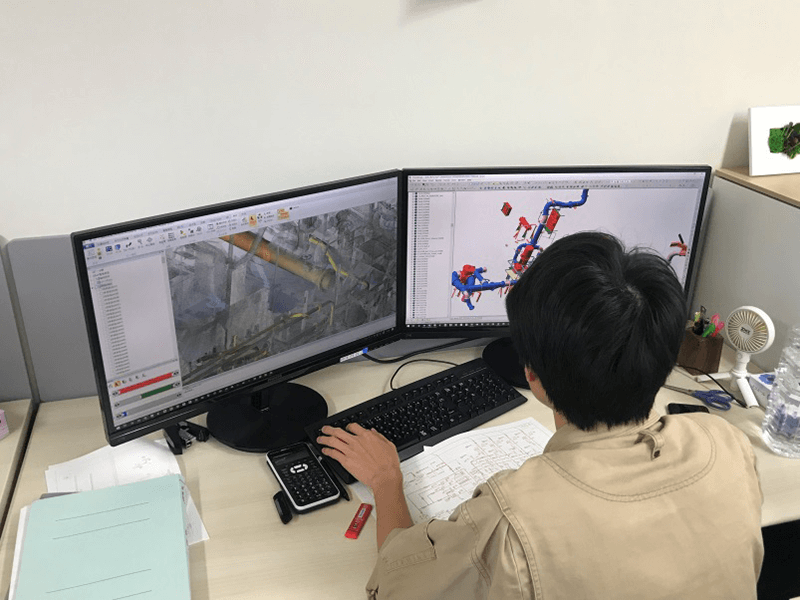
Halving construction period through improvement of 3D modeling efficiency
The introduction of ClassNK-PEERLESS has improved the efficiency of 3D modeling work, improving the accuracy of work from the 3D design stage onward and leaving time to spare. This makes it possible to accept high volumes of orders for engineering work and remodeling work that integrates all stages from design to construction, which was difficult to achieve with conventional orders.
3D design, which wasn’t available before, brought about impressive effects including reduction of interference with existing equipment, minimization of gauging work, and leveling of man-hours through cooperation with neighboring companies. In my opinion, current construction period required is only about half of what it was with 2D design.
At present, design and installation of a large SOx scrubber requires the following:
- Measurement with a 3D scanner: 8 hours (up to 300 locations to be measured)
- Modeling work using ClassNK-PEERLESS: 300 to 500 hours
- Remodeling and design (basic design, detailed design, and production design): 3,000 to 5,000 hours
As a result, high-quality design output can be provided now.
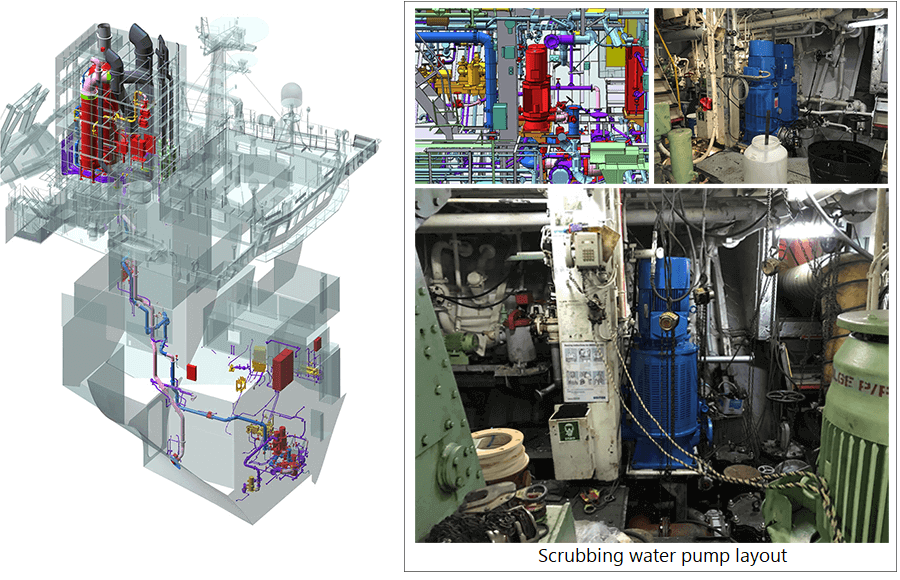
The future
If modeling work using ClassNK-PEERLESS becomes even more efficient (ultimately, if automated 3D modeling of all parts by pressing a single button becomes possible), it will probably be possible for us to use it for general repair work with tight time constraint.
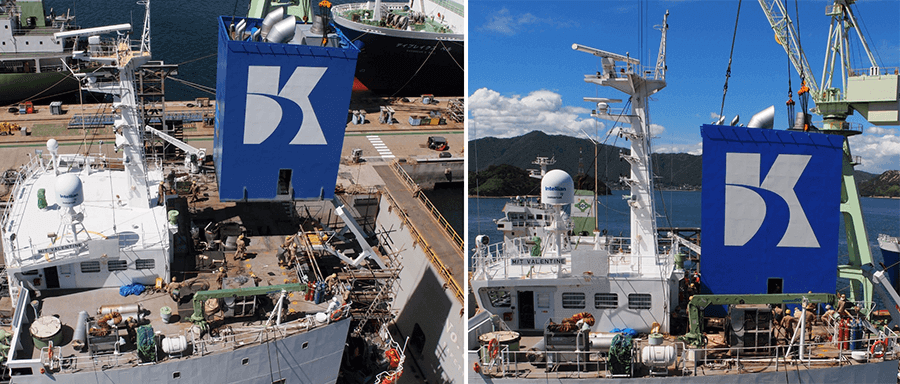
User Profile
Sanwa Dock Co., Ltd.
Headquarters | 600 Innoshimashigei-cho, Onomichi City, Hiroshima Prefecture |
URL | https://www.sanwadock.co.jp |
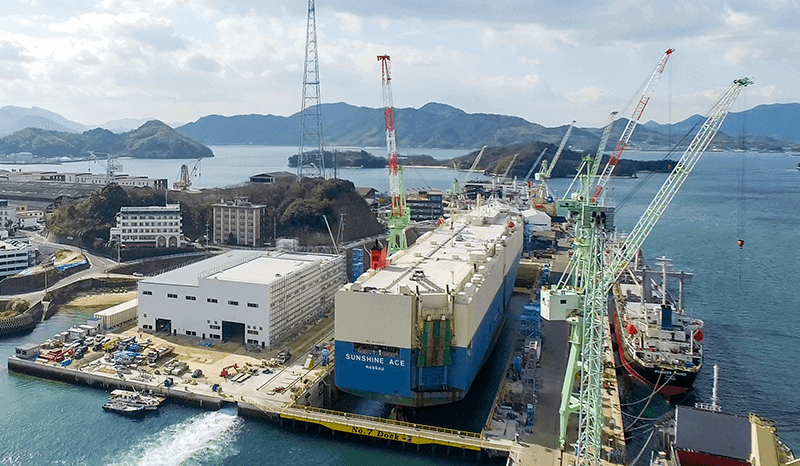
tag : User case study